You have many choices in charting a path to performance improvement (“PI”). From big consulting houses, boutique firms, to going it alone, the choices are endless.
What is the definition of “Six Sigma?”
Six Sigma is a systematic and statistically-based process to reveal defects in performance, driven generally by customer specifications. Six Sigma methodologies aim to reduce the variation and “non-value added” activity in clinical and business process which give rise to long cycle times, high cost and poor outcomes. A process that operates at true Six Sigma levels is producing acceptable quality levels over 99.9996% of the time.
Is Six Sigma a realistic goal for healthcare?
Although many healthcare processes cannot achieve such ambitious goals as implied by Six Sigma, this does not diminish the importance of the techniques. Six Sigma methodologies can substantially improve the performance of most processes, and a Six Sigma project that moves a “2 sigma” process to a “3 sigma” will have improved the performance of that process by nearly 450%.
Where does Six Sigma fit in healthcare?
Across a fairly limited number of initial pioneers we have documented nearly one hundred different Six Sigma projects that have delivered substantial gains to the organizations sponsoring the project.
Typical projects include:
- Emergency Department patient flow and cycle time
- Operating room patient flow and cycle time
- Laboratory and Radiology cycle time
- Billing, coding and reimbursement
- Supply Chain Management
- Referral Authorization
- Antibiotic Administration
More than this, however, has been the significant impact that Six Sigma has had on the culture of the sponsoring organization. Six Sigma creates a restlessness with the status quo, and a compelling force to improve how processes perform.
Why is Six Sigma gaining such attention?
There are likely a number of reasons why Six Sigma has gained so much recent attention, but none are as obvious as the struggle for healthcare organizations to overcome challenges related to quality and cost, and Six Sigma’s ability to serve both goals equally and effectively. Furthermore, healthcare organizations have been frustrated by previous efforts to improve organizational effectiveness, as any incremental gains they achieve are quickly offset by incremental reimbursement cutbacks, incremental workforce shortage, and gains that are offset by other poorly performing departments. Healthcare executives have recognized that incremental gains are not enough to compete effectively with other organizations improving at the same rate, and that only “breakthrough improvement” will relieve pressure on margins and allow for the organization to take the lead in their market.
Where is Six Sigma in use within the healthcare industry?
Six Sigma has its origins in the manufacturing industry and many leading healthcare suppliers were the first to implement it. McKesson, Standard Register, General Electric, Motorola, and Honeywell have all made significant commitments to Six Sigma, and they have reported impressive gains. More recently, blood banks have recognized the benefits of Six Sigma, a testament to its potential since blood banks are already held to extremely high standards of quality. More recently, providers and payers have adopted the principles. Many outside experts in Six Sigma believe it can have a greater impact in healthcare than any other industry.
What recognized healthcare institutions are using Six Sigma?
The list is short but growing rapidly and includes: The University of Michigan Medical Center, Yale-New Haven Health System, Mount Carmel Medical Center (Columbus OH), Charleston Area Medical Center (WV), Virtua Health (NJ/PA), Wellmark Blue Cross Blue Shield (CA), Luther Midelfort/ Mayo Health System (MN/WI), Froedert Medical Center, and Palomar Pomerado Health (San Diego CA).
What kind of track record and “ROI” has Six Sigma established in healthcare?
The typical Six Sigma project in healthcare has delivered an average of $500,000 in annualized savings. The key to Six Sigma’s impressive gains is its ability to “do more with less” and to re-deploy critical human resources where needed the most. One CEO reports that his turnover rate has actually decreased as a direct consequence of their successful Six Sigma projects.
If the ROI from Six Sigma is so compelling, why aren’t more organizations adopting it?
Fear of the unknown. Six Sigma remains a mystical technique until healthcare organizations take the time to understand its comprehensive framework. Healthcare leaders may fear their ability to gain consensus around the use of Six Sigma; they may be concerned that it is a potential “passing fad,” or too complicated to be effectively learned and applied by their staff. Finally, a significant impediment can often be the internal quality assurance infrastructure, which may feel threatened by the use of Six Sigma and its potential to overshadow their own accomplishments in the organization.
What are the key differences between Six Sigma and what I might be using now to address performance needs?
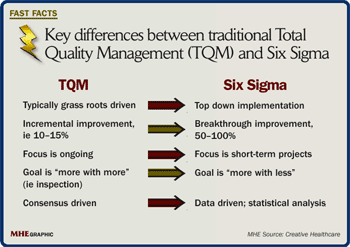
Six Sigma was not intended to replace traditional efforts at Total Quality Management or Quality Assurance, but the key differences between the methodologies have enabled Six Sigma to overcome challenges not sufficiently addressed with existing techniques.
Organizations that have implemented Six Sigma do not dispense with their existing TQM or QA functions. On the contrary, they either train these departments in the Six Sigma techniques or ensure close collaboration between these departments and Six Sigma practitioners.
Can a small or medium sized institution benefit from Six Sigma?
Absolutely. Six Sigma techniques have been effectively applied in hospitals with as few as 40 beds. Healthcare organizations generally operate most services 365 days a year, and the smallest providers still generates significant volume of activity which can be assessed and improved via Six Sigma methodologies.
Can Six Sigma be applied as an enterprise-wide initiative?
Six Sigma was designed as an enterprise-wide solution to management challenges. As many process improvement initiatives cross multiple departments, a Six Sigma practitioner inevitably must transcend different functions and departments in order to satisfy project requirements, effectively working in a “matrix” environment. It is this enterprise-wide focus that has allowed Six Sigma to accomplish such impressive gains.
Are there some departments that will benefit more from Six Sigma than others?
It was originally thought since Six Sigma originated in manufacturing, that only manufacturing oriented processes would benefit from the methodologies. However, a closer study of Six Sigma projects from that industry revealed that most projects were fundamentally “transaction” oriented, that is, dealing with the supporting processes of the manufacturer such as billing, receiving, accounts payable, supply chain management, etc. Since its arrival in healthcare, a transaction-oriented industry, the possible applications of Six Sigma have multiplied further. Not only has it been applied to the “back office” functions of the healthcare organization; Six Sigma has also been used to improve the performance of clinical processes as well.
Are there some areas where Six Sigma can have an immediate impact?
Six Sigma has its greatest impact on departments that are process-dependent rather than technology dependent. Having said this, however, Six Sigma can often improve the performance of departments that are evaluating technology investment, since no amount of technology can fix a broken process. Some of the other criteria used to determine if a project is qualified for Six Sigma include:
- Divergent views on how process is performing
- Actual performance at 2 Sigma or lower
- Suspected hidden factory and non value-added activities
- Relates to defects (quality), cycle time, yield, cost of use
- Potential to reduce defect by 70% between observed and past performance
- $175,000 initial and $500,000 future savings potential
- Candidate for disruption – approximately 4-6 months duration
- Minimum capital investment required
What kind of training and support is required for Six Sigma?
Given the remarkable impact that Six Sigma can have on an organization, it may come as a surprise to learn that the implementation can be accomplished with little disruption to the organization. Organizations can select from a pure classroom training approach, or a combination of computer-based training (CBT) augmented with a minimum of classroom time. This approach is not only more economical, but allows each student to proceed at their own pace. CBT programs can be easily customized to accommodate the personality of the sponsoring organization.
Another popular approach is to combine training with an initial Six Sigma project, led by the consulting organization that supplies the training program. This allows the organization to “train and achieve simultaneously,” and can be an effective strategy to both secure buy-in while demonstrating the impact of Six Sigma to the organization.
The key to successful implementation of Six Sigma is strong and visible senior management support. This support is critical not only to overcoming natural skepticism of Six Sigma, but to allow its participants the free reign necessary to apply its principles once training is complete.
What are typical costs for implementation?
Healthcare providers should budget $10,000-15,000 for pure classroom instruction per student and roughly half this amount if the combination CBT/classroom approach is used. Creato also offers a combined project/training approach where Creato conducts a project simultaneously with training. See above.
What are Six Sigma “blackbelts, greenbelts and yellowbelts?”
A blackbelt has completed a rigorous course of study related to Six Sigma, including approximately 120 hours of instruction, homework and examinations, and culminating in a project that has been independently reviewed and certified as substantially conforming to the principles of Six Sigma. A greenbelt has similarly completed a course of study, though less time consuming and not involving as many of the advanced statistical techniques that might be necessary for more complex projects.
Blackbelts are trained to lead and conduct multi-disciplinary projects; Greenbelts are trained to support Blackbelt projects and to complete small scale projects within their own area of expertise.
Champions or “Yellowbelts” is the designation given to senior executives that oversee the performance of Blackbelts within their organization. Finally, “Master Blackbelts” have completed a course of study to train on Six Sigma techniques, and they have also served as Blackbelts and have completed many projects. A typical Six Sigma organization will have a couple of Champions and Master Blackbelts, several Blackbelts, and a significant contingent of Greenbelts.
Why Creato?
Creato works only in the healthcare industry and is the only firm specializing in Six Sigma in healthcare. We have a unique model that maximizes the value from your investment. This includes onsite consultation to implement a Six Sigma project combined with training services to “institutionalize” the knowledge. Our approach is preferred by healthcare providers because it fits better with their culture than making Six Sigma an immediate mandate.
Creato will do the “heavy lifting” for you by lifting the burden from your shoulders and doing the first project for you. We will concurrently train your people; effectively “fishing for you” while teaching your staff “how to fish.” This accelerates the ROI without distracting your people from their principle tasks.
Unlike other consultants, we do not leave the engagement until results are implemented and improvements realized. Unlike other consultants, we do not wish to be a barrier to the knowledge and will assist your organization to learn the principles on a timetable that is comfortable and accommodating to your current workload. We will not force you to attend classroom sessions but will base our training program in a state-of-the-art CBT.
How do we usually begin an evaluation?
We are happy to come onsite to present the principles of Six Sigma and options for moving forward. We simply ask that – in light of current travel environment – that your decision making team is assembled and prepared to give a response to a proposal within a reasonable timeframe.
We will issue a proposal shortly after an onsite visit, which would include both the initial presentation and a series of interviews. This will allow us to craft the proposal you will ultimately receive. Projects take 6-8 months and involve a team of 2 consultants, with a minimum of one certified blackbelt. Monthly client contact ensures you are up to date on our activities.
What if we don’t know the project opportunity?
This is a common situation and an ideal one for Creato since we have so much healthcare and Six Sigma experience. The Six Sigma methodologies include “scoping tools” that will direct us to the most appropriate opportunity. Upon the close of the definition stage you will be presented with the details of this opportunity and the option to cancel the project or to approve continued work on it. By this time you will have been exposed to Six Sigma’s initial process for project management, the competency of our staff, and the project opportunity we believe exists. You will be in an excellent position to evaluate Six Sigma’s potential and our ability to maximize its impact on your organization.
How can I learn more?
Creato offers many free resources on its website. We also offer a free “Capability Analysis” in a determination of whether your organization might benefit from Six Sigma programs and projects. Contact Creato for more details.