For most organizations, up to 25% of revenues are consumed by waste. Each 10% reduction in wasteful activity can contribute as much as 2.5% to their bottom line.
Lean Sigma Learning Lab
Lean Sigma helps you accelerate the performance of your current processes and has a multitude of applications. Our LEAN course includes real world case studies, tools and templates and everything else you need to put the powerful concepts of LEAN to immediate use.
Register Online
Price per student: 1,495.00
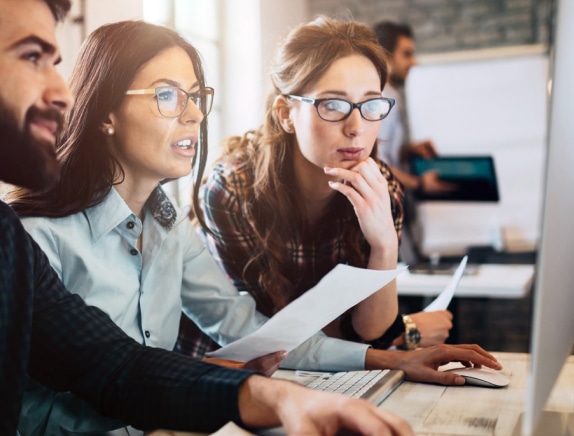
- Web-Based Training
- Focused on Applying LEAN
- Includes real world case studies
- Includes all necessary project tools
- Accredited by the Council for Six Sigma Certification
Here Is What You Will Learn
Look through our Table of Contents to see more information.
Introduction to Quality and Performance Improvement
- A Very Brief History of Quality
- Key Points of Improvement Methods
- Basic Principles of Quality
- Basic Principles of PI
- Cost of Poor Quality (COPQ)
- Costs of Quality
- Many Methodologies
- Deming and Juran
- Deming’s Fourteen Points
- Tools: PCDA
- The Pioneers
- The Juran Trilogy
- Juran’s Analogy
- Six Sigma Concept
- Six Sigma Emphasizes
- Six Sigma Characteristics
- Six Sigma Approach
- Lean
- Lean Six Sigma
- Value Stream Management
- Rough Comparison of Approaches
Introduction to Lean
- What is Lean?
- Steps in Lean
- Steps in Lean and DMAIC
- What Is Lean Thinking?
- Staff Worried About the Intent?
- Waste According to Toyota’s Taiichi Ohno
- Get Rid of the Waste
- Value-Added Steps
- Examples of Muda
- Five Principles of Lean Thinking
- Value
- An Example of Value
- The Critical to Quality Tree
- Viewpoint: Who is the Customer?
- What is a Value Stream?
- Value Stream
- Value Stream Map Example
- Flow
- Contrasting “Flow” and “Batch”
- Flow of Work
- Bottlenecks
- Hand-offs
- Pull
- Perfection
Six Sigma and Lean Linkages
- Comparing Six Sigma and Lean
- What Does “Six Sigma” Mean?
- Definition #1: Six Sigma is a Statistical Measure of Quality
- Why 3.4 Parts Per Million?
- Definition #2: Six Sigma is a Problem Solving Methodology
- Definition #3: Six Sigma is a Management Philosophy
- Lean Thinking and Six Sigma
- The Steps of DMAIC
- Linkages
- Lean Metrics
- Short Term and Long Term Six Sigma and Lean
General Lean Concepts
- What is Wanted?
- The Basic Tenets of Lean
- Toyota Production System
- MUDA in TPS
- The 8th Waste
- Six Rules for Lean (Toyota)
- Basic Image of Lean Production (Toyota)
- Customer Focus
- Stability
- Stable vs. Capable
- Standardization/Standard Work
- Elements of Standard Work
- Just-in-Time Production
- Jidoka
Tools and Techniques
- The Right Process Will Produce the Right Results
- Seven Types of Muda (Waste)
- Visual Management
- Make it Obvious to the Eye
- Visual Controls
- Elements of Standard Work
- The 5S Technique and Visual Management
- The “5’s”
- Lean and Six Sigma Tools for Operation Excellence
- Sort, Set and Shine
- Standardize and Sustain
- Scan – the Pre-5S Step
- Other Considerations for 5S
- Remember the Kanban?
- Kanban Example
- Buffer and Safety Stock
- In-Process Stock
- Pitch and Lot Size
- Takt Time and Staffing
- The “Real” World
- Takt Time vs. Cycle Time
- Little’s Law and Lead Time
- Heijunka (Load Leveling)
- Example of Heijunka Box
- Example – Balancing
- Just In Time
- Work Sequence
- Work Layouts
- Example – Work Sequence/Layout
- Total Productive Maintenance
- Poka-Yoke
Common Cause and Special Cause Variation
- “Fix or Six”
- How Lean Fits In
- Control Charts
- Common Cause Variation
- Special Cause Variation
- Special Causes and Cases
- Trends, Shifts and Cycles
- Control Chart Example
- Control Charts and “Fix or Six”
- Misinterpreting Data
- Control Chart Example
- What Should Managers Do?
- Variation Management Paradox
- Management Using Control Charts
Selecting Lean Projects
- Elements for Successful Projects
- “Ideal” Projects
- But What Do I Really Need?
- Problems In Project Identification
- Lean Is Supposed to be Faster
- Questions to Ask (and Answer)
- Project Selection and Rating Tool
- Exercise
- Implementation – Must Haves
- Barriers to Implementation
Lean Project Definition and Goals
- The Lean Approach
- Team Charter
- Elements of A Good Charter
- The Business Case
- Business Case Example
- Project Scope
- Scope Examples
- Project Scope Guidelines
- Problem Statement Elements
- Comprised of Two Statements
- Problem Statement Evolution
- Problem Statement Examples
- The SIPOC
- Whate is a Process?
- Steps in Using the SIPOC
- Problem Statement in Coordination with the SIPOC
- Picture Frame
- Using the Picture Frame
- Goals/Objectives
- Goals and Objectives Example
- Milestones
- Roles/Responsibilities
- Team Charter Template
Customer Focus
- Service-Profit Chains and Customers
- In Any Process…
- Roles May Change
- Customers, Needs and Requirements
- Know What A Customer Is
- External Customer
- Internal Customer
- Cautions
- Segment Customers (If Necessary)
- Customer Needs Do Not Equal Customer Requirements
- Prioritize the Customer Requirements
- The (Noriaki) Kano VOC Model
- Using The Kano Model: Must-Be
- Using The Kano Model: 1-Dimensional
- Using The Kano Model: Delighters
- Kano Model “Migration”
- “Kano’s” Model – Examples
Current State
- What Is the Current State?
- First Things First
- Different Types of Process Maps
- Process Mapping Symbols
- Process Mapping Example
- Process Observation
- Other Considerations
- Work Flow/Spaghetti Diagrams
- Work Flow Diagram Example
- Work Flow Diagrams
- Relationship Mapping
- The Relationship Table
- Medication Process: Current Relationship Map
- Swim Charts
- Swim Chart Example
- Value Stream Mapping (VSM)
- What Are We Looking For?
- Relationship Diagram into Value Stream Mapping
- Basic Layout of Current State VSM
- General Guidelines for VSM
- Step 1: Customer Consumption
- Step 2: Flow of Materials
- Step 3: Supplier Information
- Step 4: Push Arrows
- Step 5: Information Flow
- Disconnects
- Step 6: Time Line
- Time Measurement
- Why Fewer Samples in Lean?
- VSM Signs of Waste
- What VSM’s Don’t Reveal
- Value Analysis
- Value-Added Steps
- Non-Value-Added Steps
- Value/Non-Value Grid
- Example of Completed Grid
- Value-Added Line
- Value Stream – Neurology
- Value Analysis Example
- Relationship Map
- Some Questions to Think About
- Example – Project Background
- Example – Swim Chart
- Value Stream Map – Current State IP X-Ray Throughput
- Example – Value Analysis: Subprocess Map
Designing the Future State
- Designing the Future State
- What is a “Future State?”
- Needs
- Begin Designing the Future State
- Tools and Concepts
- Future State Questions
- Customer Needs
- What Does the Customer Really Need?
- Takt Time and Staffing
- Lead Time and Cycle Time
- Pitch and Lot Size
- Checking Performance
- How Often Will You “Check?”
- Mistake-Proofing
- When You Can’t Error Proof
- Visual Management
- Visual Controls
- Information Overload
- Example – Monitoring
- Maximize Value
- Steps in Value Analysis
- Defining the Value Stream
- Value-Added Steps
- Non-Value-Added Steps
- Non-Value Added (NVA) Classes
- Disconnects
- Swim Chart With NVA Analysis
- Value Analysis Example
- Relationship Maps: As-is vs. “Might be”
- Decreasing Work Interruptions
- Flow of Work
- Interruptions
- Just-in-Time Production
- Kanban
- Kanban Example
- Work Sequence
- Work Layouts
- Centralization or Decentralization?
- Example – Work Sequence/Layout
- Balancing Workload
- Load Leveling
- Example – Balancing Work
- Which Improvements?
- What Improvements Will Be Needed?
- A Useful Place to Start
- Standard Operating Procedures
- The 5S Technique
- 5S: Standardization and Organization
- The 5 Whys
- Example – The 5 Whys
Selecting and Piloting Your Lean Project Solutions
- Problem-Solving Approaches
- Improvement Implementation
- Improvement Work Plan
- Breaking it Down
- Prioritizing Improvements
- Kaizen
- Pilot Implementation
- Pilot Implementation Activities
- Pilot Follow-Up
- Example: Exchange Cart
Controlling and Sustaining
- Implementation – Must Haves
- Barriers to Implementation
- Ensuring Acceptance
- Stakeholder & Resistance Analysis
- Sustaining Gains Through Control Plans
- What Is A Control Plan?
- The Control Plan Tightrope
- Control Plan – Example
- Control Plan: Supplements
- Other Documentation
- Statistical Process Control (SPC)
- Decision Rules
- New Control Limits?
- Control Chart Example
- Common Pitfalls
- Audit Process
- Auditing a Process
- Corrective Action
- Designing the Control Plan
- Project Closure and Handoff
- When to “Get Out”
- Disbanding the Team
Bonus Module: Human Factors and Usability
- What Are Human Factors?
- Why Human Factors?
- Taking Human Factors Into Account
- Donald Norman
- Some Factors Affecting Performance
- What Can Go Wrong?
- Usability: ISO 9000 Standards
- Usability
- Usability: The 5 E’s
- Case Example: OR Suite Set-Up
Case Studies
- Reducing Wait Times in a GI Clinic
- Timely Receipt of Admission Orders
“I am TRULY enjoying the course! It is very well-written, concepts are easy to follow and master, and the content is accurate. I’ve worked in CQI/Performance Excellence since 1987, but your course is a great refresher and applicable to my current work in healthcare. Thank you.”
Yvonne Simmons Howze, PhDKellogg National Leadership FellowASQ CMQ/OE
St. Augustine, Florida